Get Fast and Efficient Packaging Machine Repair for Your Production Line
Quick and Reliable Packaging Maker Repair Solutions to Reduce Downtime
In the competitive landscape of production, the effectiveness of packaging procedures hinges on the reliability of machinery. Quick and reliable fixing services are essential in mitigating downtime, which can lead to significant functional problems and financial losses.
Importance of Timely Repairs
Timely repair services of product packaging equipments are vital for keeping operational performance and lessening downtime. In the fast-paced atmosphere of production and packaging, even minor malfunctions can result in significant delays and productivity losses. Resolving problems without delay guarantees that makers run at their optimum capability, thus safeguarding the circulation of operations.
Furthermore, timely and routine maintenance can prevent the acceleration of small issues right into major failures, which usually incur higher repair expenses and longer downtimes. An aggressive technique to equipment repair work not only maintains the honesty of the tools yet likewise boosts the total reliability of the production line.
Furthermore, prompt fixings add to the durability of product packaging equipment. Machines that are serviced promptly are much less likely to deal with excessive deterioration, permitting businesses to maximize their financial investments. This is particularly important in sectors where high-speed packaging is vital, as the demand for consistent performance is critical.
Advantages of Reliable Provider
Dependable service companies play a pivotal duty in making sure the smooth operation of product packaging makers. Their competence not only improves the effectiveness of repair services yet also contributes substantially to the longevity of tools.
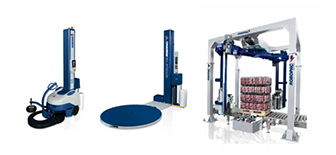
Additionally, a reputable solution copyright provides detailed support, consisting of training and advice for personnel on equipment procedure and upkeep finest practices. This not just encourages staff members yet additionally cultivates a society of security and effectiveness within the organization. On the whole, the benefits of involving reliable company extend past prompt repairs, positively affecting the whole functional workflow of packaging processes.
Usual Packaging Equipment Concerns
In the realm of product packaging procedures, numerous concerns can jeopardize the performance and capability of devices (packaging machine repair). An additional common problem is imbalance, which can create jams and unequal packaging, influencing item high quality and throughput.
Electric problems can likewise interrupt packaging procedures. Damaged wiring or malfunctioning sensors may result in erratic maker behavior, causing delays and increased functional expenses. In addition, software glitches can hinder the machine's shows, resulting in operational inadequacies.
Irregular item circulation is an additional critical concern. This can arise from variants in item form, weight, or size, which may affect the device's ability to handle products precisely. Inadequate training of operators can aggravate these problems, as untrained employees might not identify very early indicators of malfunction or might abuse the tools.
Resolving these usual product packaging device problems promptly is necessary to maintaining performance and making sure a smooth operation. Normal evaluations and proactive upkeep can dramatically alleviate these concerns, promoting a trusted packaging setting.
Tips for Lessening Downtime
To minimize downtime in product packaging operations, over at this website carrying out an aggressive upkeep technique is critical. Frequently scheduled maintenance checks can recognize potential issues before they intensify, ensuring devices run effectively. Developing a routine that includes lubrication, calibration, and examination of critical elements can significantly reduce the regularity of unanticipated breakdowns.
Training staff to run equipment correctly and acknowledge early indication of malfunction can likewise play an important duty. Empowering drivers with the expertise to carry out standard troubleshooting can stop small problems from creating major delays. In addition, keeping a well-organized supply of necessary extra parts can expedite repair services, as awaiting components can result in extended downtime.
Additionally, recording equipment efficiency and upkeep tasks can assist identify patterns and recurrent issues, enabling targeted interventions. Integrating innovative tracking technologies can offer real-time information, enabling predictive upkeep and decreasing the danger of sudden failings.
Finally, fostering open interaction between operators and upkeep teams ensures that any kind of irregularities are promptly reported and resolved. By taking these proactive procedures, organizations can enhance functional effectiveness and dramatically reduce downtime in product packaging procedures.
Picking the Right Repair Solution
Selecting the appropriate fixing service for packaging devices is a critical decision that can considerably impact operational effectiveness. A well-chosen service supplier ensures that your machinery is repaired swiftly, efficiently, and to the highest possible criteria. Begin by examining the provider's experience with your details sort of product packaging tools. A specialist acquainted with your machinery can identify issues a lot more precisely and carry out options extra quickly.
Next, think about the provider's credibility. Seeking feedback from other services within your market can offer understandings right into dependability and top quality. Qualifications and collaborations with acknowledged devices producers can likewise suggest a commitment to excellence.
Furthermore, analyze their reaction time and availability. A company that can use prompt support reduces downtime and keeps production circulation constant. It's also important to my website ask about warranty and service guarantees, which can show the self-confidence the company has in their you can look here job.
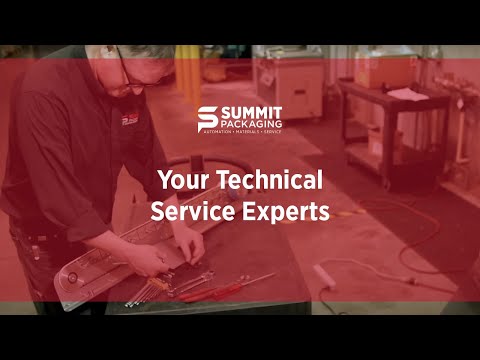
Conclusion
Finally, the importance of reliable and quick packaging machine repair service solutions can not be overstated, as they play an essential function in lessening downtime and guaranteeing operational efficiency. By focusing on prompt repair work and picking dependable service suppliers, businesses can properly attend to typical concerns and maintain performance. Carrying out aggressive maintenance methods and buying personnel training further enhances the longevity of packaging machinery. Ultimately, a tactical strategy to fix solutions cultivates an extra resilient production setting.
Prompt repairs of product packaging makers are essential for maintaining functional efficiency and decreasing downtime.Furthermore, prompt repair work add to the longevity of packaging machinery. On the whole, the benefits of engaging reliable service suppliers prolong past immediate repair services, favorably affecting the entire functional workflow of product packaging procedures.
